Bring Out The Right Shape And Size With The Help Of Suitable Cutters
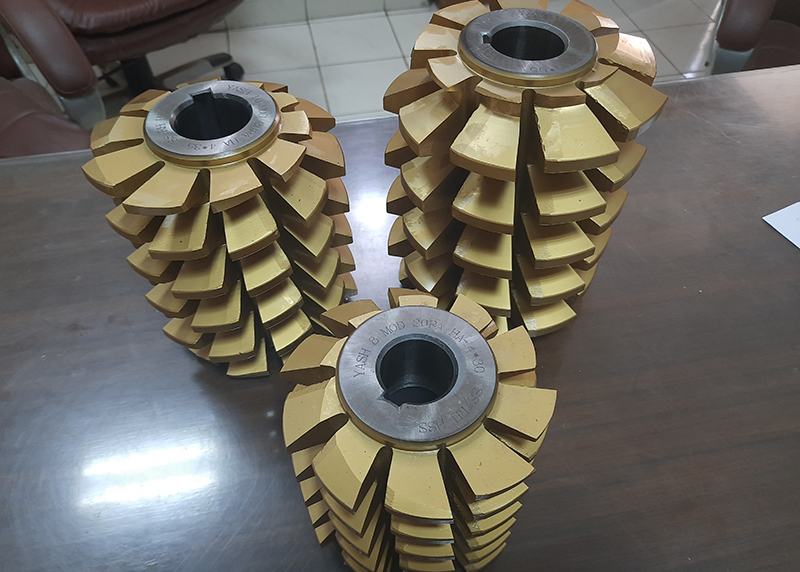
Several metals can be shaped into the proper sizes using gear cutters with sharp edges of precise proportions. Mechanical professionals widely use these tools for a variety of activities. They are a crucial component of milling machines, which aid in cutting metal and producing gears with the proper dimensions. They work well when used with Gear Hobs to complete the process. So you need to meet the right gear hob cutters supplier. The fact that hobs are tools that come in various sizes and forms is widely known. One of the most significant and well-liked shapes is spherical with sharp edges.
Different shapes:
Before purchasing the teeth, make sure the diameter is appropriate for shaping metal into the necessary shape. The applications for which a machine is being used must be carefully considered while making decisions in retrospect. You must find a good gear-cutting manufacturer carrying the various tools listed above. Before buying the finished item, you should thoroughly review the catalogues.
The cutting process is assessed based on several factors. In order to perfect metals for your intended use, you must take into account how many sharp edges a gear cutter has. This operation requires a lot of force, particularly when working with heavy metal. In numerous cases, this technique has resulted in machine wear and tear. The cutter is coated with a protective coating of carbonic compound to address this problem and make it more resistant to greater temperatures.
Simple to follow the design:
Gear hobs, particularly resistant to these phenomena, can benefit from the coating’s ability to prolong lifespan. To create teeth with the right diameter, you must measure the hobs’ length. To make sure you pick the finest choice possible, you should consult the gear cutting tools manufacturers‘ handbook, which includes specs and relevant diagrams. A similar method can be applied to selecting ideal endmills.
You can select instruments with many teeth or flutes if the metal is large, which will facilitate smooth cutting. Tool gear is sometimes called the infrastructure needed to create performance and debugging tools. They gather data about particular program lines. This data is arranged and intuitively shown to users via the Tool Gear viewer. They come in various shapes, including a polygonal construction that facilitates the carving of intricate metals.
Conclusion:
The initial purpose of tool gear was to provide an interface for reading and inputting dynamic instruments. An interface for dynamically instrumenting applications is available in Tools Gear. Tool gear can identify all the locations where it can insert instrumentation and start a serial or parallel program. To ensure that the cutters created can deliver the intended result, the companies that manufacture these gear-cutting tools consider the gear finishing and verify a specified set of standards by the client’s specifications. This technique is very technical, and the cutters are expected to provide results that meet high standards. High-precision tools are more favoured in heavy industries than other tools.